Round-the-clock mozzarella operations with driverless forklift truck
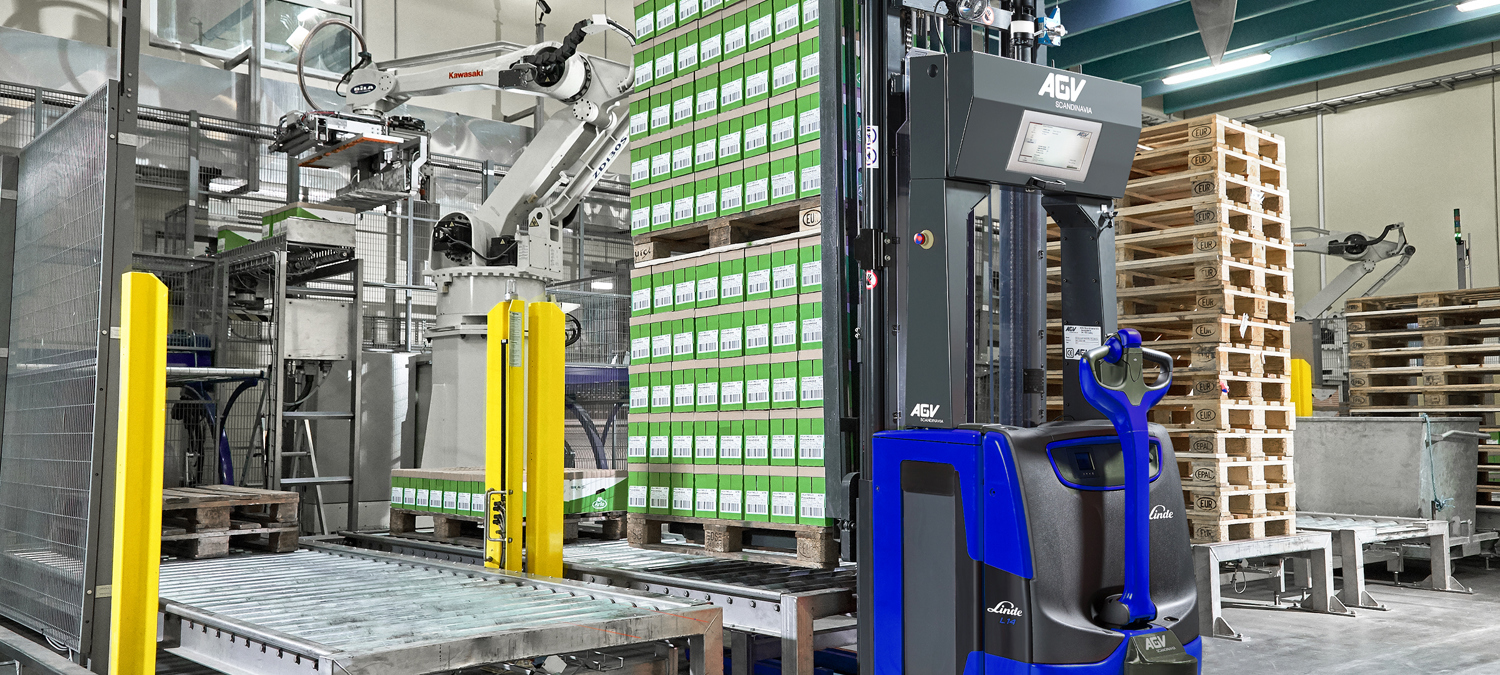
Added value in the supply chain
For Arla Foods in Rødkærsbro, Global AGV has supplied an AGV solution based on a driverless forklift truck. The self-propelled forklift truck is on regular service in the warehouse, where it collects pallets with stacked cardboard boxes and safely transports them to a conveyor belt, which then sends the pallet to a stretch wrapper. The process takes only a few minutes and continues around the clock.
More pallets are
loaded in less time
Improved
work environment
Shorter
delivery time
LEAN
optimisation
Challenge
For Arla Foods, it is essential that the entire production process contributes to enhancing the value of the final delivery to customers. The implementation of an AGV solution in the warehouse helps optimise internal flow across production, quality control, logistics, and storage.
Solution
The driverless truck takes care of itself and smoothly navigates well-defined routes from A to B. It's easy, simple, and straightforward. Without much hassle, the route or other functions can be changed, allowing the AGV solution to be adapted to the task at hand.
Gain
The AGV optimises internal transport in production, playing a crucial role in this workflow. Meanwhile, employees who used to handle the transport task can now engage in more value-added tasks.
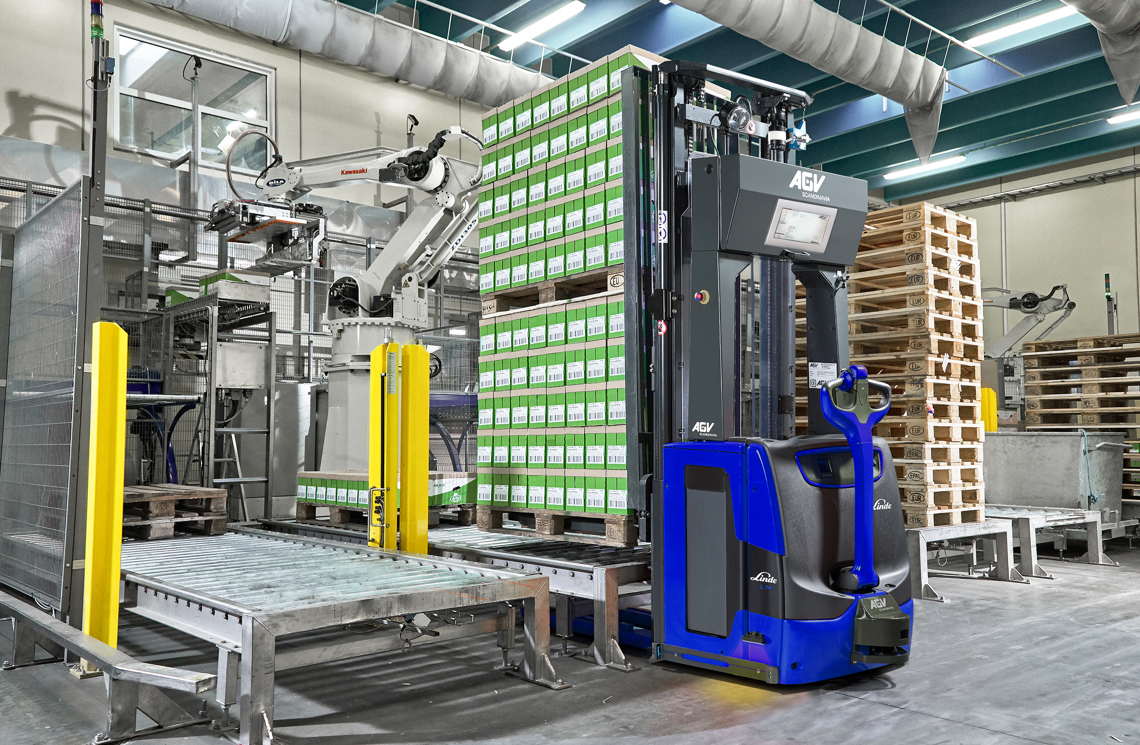
Added value to the supply chain
For Arla Foods, it is essential to see the entire production cycle as a total value chain, where all stages of the process contribute to increasing the value of the final delivery to customers. The AGV solution in the warehouse is fully in line with Arla Foods’ desire to optimise the internal flow with production, control, internal logistics, warehouse, etc.:
“The AGV solution is a great example of added value in the total production flow. The self-propelled forklift truck pretty much takes care of itself and runs smoothly on well-defined routes from A to B. It’s easy, simple and straightforward. Without much effort, we can change the driving route or other functions so that the AGV solution can be adapted if it needs to drive longer or to stack in new ways,”
Allan Poulsen, team manager at Arla Foods in Rødkærsbro
Sensors along the route
The AGV orients itself with mounted sensors that talk to other sensors along the driving route and the conveyor belts. The base machine is a standard truck that has been implemented with advanced hardware and software on the machine, so it can navigate a well-defined driving pattern at the Arla warehouse. The route is set by manually driving the forklift truck along the route and coding it based on selected positions along the way.
More perspectives
The AGV solution was put into operation in December 2016 and the machine has been running flawlessly ever since.
“We have had good experiences with the AGV solution. We can see that it works when moving products according to a fixed pattern. This way, it does its job and frees up resources from the internal logistics. I can see some perspectives on this, which could, for example, extend its operating range to a few more locations in the warehouse,” states team leader Allan Poulsen.
The driverless AGV truck optimises internal transport in production and thus performs an important task in this flow. At the same time, the employees who previously handled transport tasks can instead perform more value-adding tasks.
Interested in learning more about Global AGV?
Send us a message, and we'll look at the possibilities.
Or call us at +45 96 69 47 10.
Contact us
We are ready to answer all your
questions and discuss all the possibilities
of production optimisation in your company.